Different working conditions and material handing, need to select the right material for your crusher wear parts.
1. Manganese Steel: which is used to cast jaw plates, cone crusher liners, gyratory crusher mantle, and some side plates.
The wear resistance of manganese steel with an austenitic structure is attributable to the phenomenon of work hardening. The impact and pressure load result in a hardening of the austenitic structure on the surface. The initial hardness of manganese steel is approx. 200 HV (20 HRC, hardness test according to Rockwell). The impact strength is approx. 250 J/cm². After the work hardening, the initial hardness can thereby increase to an operational hardness of up to approx. 500 HV (50 HRC). The deeper-set, not yet hardened layers thereby provide for the great toughness of this steel. The depth and hardness of the work-hardened surfaces depend on the application and type of manganese steel. The hardened layer penetrates down to a depth of approx. 10 mm. Manganese steel has a long history. Today, this steel is used mostly for crusher jaws, crushing cones, and crushing shells.
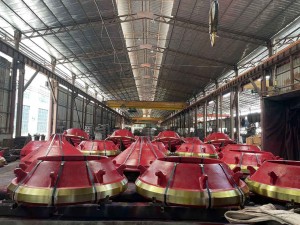
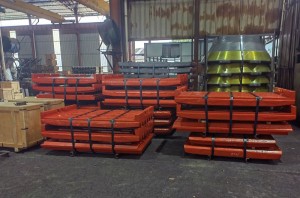
2. Martensitic Steel which is used to cast impact crusher blow bars.
Martensite is a completely carbon-saturated type of iron that is made by quick cooling-off. It is only in the subsequent heat treatment that carbon is removed from the martensite, which improves the strength and wears properties. The hardness of this steel ranges between 44 to 57 HRC and the impact strength is between 100 and 300 J/cm².Thus, with regard to hardness and toughness, martensitic steels lie between manganese and chrome steel. They are used if the impact load is too little to harden the manganese steel, and/or good wear resistance is required along with good impact stress resistance.
3. Chrome Steel which used to cast impact crusher blow bars, VSI crusher feed tubes, distribute plates…
With chrome steel, the carbon is chemically bonded in the form of chromium carbide. The wear resistance of chrome steel is based on these hard carbides of the hard matrix, whereby the movement is hindered by offsets, which provides for a high degree of strength but at the same timeless toughness. To prevent the material from becoming brittle, the blow bars must be heat-treated. It must thereby be observed that the temperature and annealing time parameters are exactly adhered to. Chrome steel typically has a hardness of 60 to 64 HRC and a very low impact strength of 10 J/cm². To prevent breakage of chrome steel blow bars, there may not be any unbreakable elements in the feed material.
4. Alloy Steel which is used to cast gyratory crusher concave segments, jaw plates, cone crusher liners, and others.
Alloy steel also widely use in casting crusher wear parts. With this material, the crushed material can be dressed by magnetic separation. However, alloy steel crusher wear parts are easily broken, so this material can not use to cast the largest parts, only suit to cast some small parts, weigh less than 500kg.
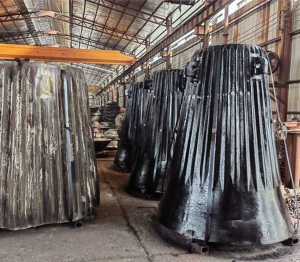
5. TIC Inserts Crusher Wear Parts, that TIC inserts alloy steel is for cast jaw plates, cone crusher liners, and impact crusher blow bars.
We use titanium carbide bars to insert crusher wear parts to help wear parts get more good working life when crushing hard material.
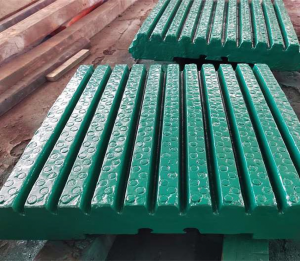
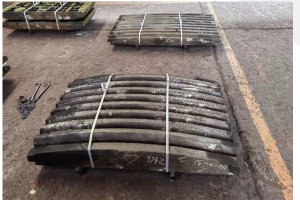
For more information, pls contact us.
Post time: Dec-01-2023